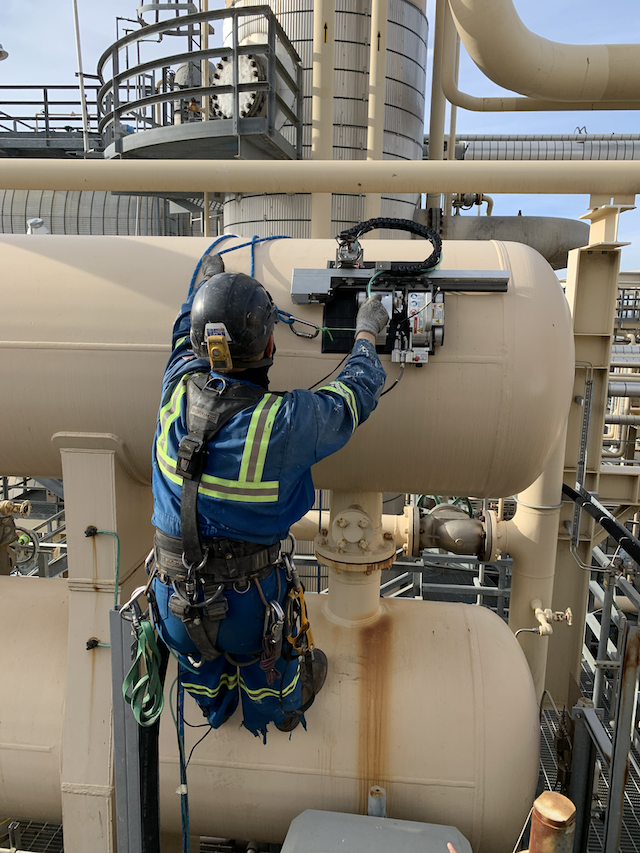
Nondestructive Examination – Advanced
HSI provides advanced nondestructive examination services to its clients that enable them to determine the quality and condition of a material without damaging it. This process has many different methods, such as thermal imaging, visual inspection, X-ray radiography, magnetic particle testing, ultrasonic testing and eddy current testing. These services are used to detect flaws, cracks, corrosion, and other anomalies in materials used for construction or manufacturing. HSI can also provide scanning services that identify potential safety risks associated with the usage of a material. These include identifying weak points that may not be visible to the naked eye to provide guidance for remediation activities. By using advanced nondestructive examination techniques, HSI is able to help its clients find problems before they become costly failures. With their expertise in this field, HSI SMEs help to ensure that their clients adhere to safety standards while avoiding unnecessary costs and losses.